Средство визуального отображения информации в бережливом производстве: Visualization — творческий способ применить Lean
if(rtbW>=960){var rtbBlockID="R-A-744041-3";} else{var rtbBlockID="R-A-744041-5";}
window.yaContextCb.push(()=>{Ya.Context.AdvManager.render({renderTo:"yandex_rtb_7",blockId:rtbBlockID,pageNumber:7,onError:(data)=>{var g=document.createElement("ins");g.className="adsbygoogle";g.style.display="inline";if(rtbW>=960){g.style.width="580px";g.style.height="400px";g.setAttribute("data-ad-slot","9935184599");}else{g.style.width="300px";g.style.height="600px";g.setAttribute("data-ad-slot","9935184599");} g.setAttribute("data-ad-client","ca-pub-1812626643144578");g.setAttribute("data-alternate-ad-url",stroke2);document.getElementById("yandex_rtb_7").appendChild(g);(adsbygoogle=window.adsbygoogle||[]).push({});}})});
window.addEventListener("load",()=>{
var ins=document.getElementById("yandex_rtb_7");if(ins.clientHeight =="0"){ins.innerHTML=stroke3;}},true);
Бережливое производство — Визуализация
if(rtbW>=960){var rtbBlockID="R-A-744041-3";} else{var rtbBlockID="R-A-744041-5";}
window.yaContextCb.push(()=>{Ya.Context.AdvManager.render({renderTo:"yandex_rtb_6",blockId:rtbBlockID,pageNumber:6,onError:(data)=>{var g=document.createElement("ins");g.className="adsbygoogle";g.style.display="inline";if(rtbW>=960){g.style.width="580px";g.style.height="400px";g.setAttribute("data-ad-slot","9935184599");}else{g.style.width="300px";g.style.height="600px";g.setAttribute("data-ad-slot","9935184599");} g.setAttribute("data-ad-client","ca-pub-1812626643144578");g.setAttribute("data-alternate-ad-url",stroke2);document.getElementById("yandex_rtb_6").appendChild(g);(adsbygoogle=window.adsbygoogle||[]).push({});}})});
window.addEventListener("load",()=>{
var ins=document.getElementById("yandex_rtb_6");if(ins.clientHeight =="0"){ins.innerHTML=stroke3;}},true);
Принцип визуализации является базовым принципом Lean, успешно применяемым уже на протяжении второго столетия в различных формах. Он основан на особенности устройства человеческого организма, которое заключается в наибольшей восприимчивости информации человеком через органы зрения.
Как известно, зрительный нерв человека – самый толстый нерв в организме, он мгновенно передаёт информацию в головной мозг. Человек воспринимает 83% информации, которую он видит и только 11% — которую слышит, 3,5% информации, которую он нюхает, 1,5% информации, которую он пробует на вкус и 1% информации, которую он ощущает.
Что касается запоминания информации человеком, то тут картина немного иная: человек запоминает 20% того, что он слышит, 30% того, что он видит, 50% того, что он одновременно слышит и видит, 70% того, что он говорит и 90% того, что он внедряет.
Визуализация, т.е. метод представления информации в виде оптического изображения (рисунков, диаграмм, графиков, структурных схем, карт, таблиц и т. д.), является наиболее простым и эффективным способом передачи информации.
Наиболее часто используемые методы визуализации:
1) Оконтуривание
2) Цветовая маркировка
3) Метод дорожных знаков
4) Маркировка краской
5) «Было»-«стало»
6) Графические рабочие инструкции
7) Доска почета отличившихся сотрудников
Требования к средствам визуального контроля:
- описывают потенциальные неисправности и возможные остановки в работе;
- просты для понимания, учитывают разный уровень образованности и владения языками;
- видны издалека;
- содержат актуальную информацию, обновляются периодически и своевременно;
- понятны с первого раза.
Направления развертывания:
- Визуализация мест хранения, маркировки, указателей
- Визуализация стандартов работ, правил, подсказок
- Визуализация техники безопасности
- Визуализация технических проблем, остановки оборудования, необходимости помощи
- Визуализация заданий, планов работ, графиков
- Визуализация целевых показателей, текущего состояния
- Визуализация хода отдельных проектов, мероприятий
if(rtbW>=960){var rtbBlockID="R-A-744041-3";} else{var rtbBlockID="R-A-744041-5";}
window.yaContextCb.push(()=>{Ya.Context.AdvManager.render({renderTo:"yandex_rtb_5",blockId:rtbBlockID,pageNumber:5,onError:(data)=>{var g=document.createElement("ins");g.className="adsbygoogle";g.style.display="inline";if(rtbW>=960){g.style.width="580px";g.style.height="400px";g.setAttribute("data-ad-slot","9935184599");}else{g.style.width="300px";g.style.height="600px";g.setAttribute("data-ad-slot","9935184599");} g.setAttribute("data-ad-client","ca-pub-1812626643144578");g.setAttribute("data-alternate-ad-url",stroke2);document.getElementById("yandex_rtb_5").appendChild(g);(adsbygoogle=window.adsbygoogle||[]).push({});}})});
window.addEventListener("load",()=>{
var ins=document.getElementById("yandex_rtb_5");if(ins.clientHeight =="0"){ins.innerHTML=stroke3;}},true);
Основные преимущества инструмента:
- возможность значительно упростить работу, сэкономить время, энергию и деньги;
- предоставление информации о плановых показателях, которых нужно достичь, наличии необходимых в работе материалов и месте выполнения тех или иных работ;
- увеличение производительности;
- помощь руководителю в определении состояния процесса, в выявлении узких мест в производственных процессах и операциях, возможности оперативно принимать корректирующие меры;
- поднятие коллективного духа и моральное стимулирование работников.
Применение инструментов и методов бережливого производства позволяет добиться значительного повышения эффективности деятельности предприятия, производительности труда, улучшения качества выпускаемой продукции и роста конкурентоспособности без значительных капитальных вложений.
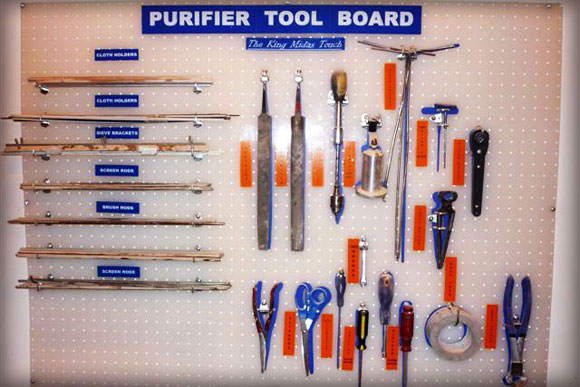
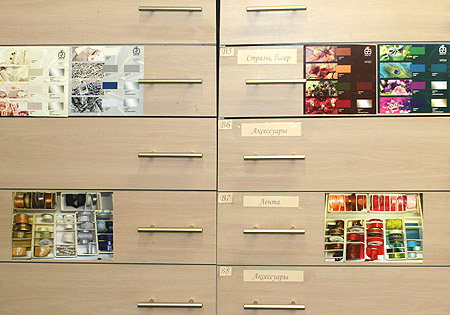
Инструменты 5S. Визуализация | WKazarin.ru
Визуализация – неотъемлемая составляющая 5S, с помощью которой можно с одного взгляда понять, насколько глубоко удалось продвинуться в улучшении рабочих мест и повышении производственной культуры. Визуализация нужна и на производствах, особенно там, где используется большой спектр материалов и компонентов, и в офисе, в котором главным “рабочим материалом” является информация.
Визуализация в 5S нужна, чтобы каждый мог мгновенно отличить нормальное состояние (дел, процесса, рабочего места) от ненормального.
Визуализация запасов
Любая видимая ненормальность при этом становится очевидной целью для улучшений.
На разных этапах внедрения 5S используются разные подходы к визуализации, но задача остается одной и той же: любой человек должен легко определить, все ли в порядке в рабочей зоне.
if(rtbW>=960){var rtbBlockID="R-A-744041-3";} else{var rtbBlockID="R-A-744041-5";}
window.yaContextCb.push(()=>{Ya.Context.AdvManager.render({renderTo:"yandex_rtb_4",blockId:rtbBlockID,pageNumber:4,onError:(data)=>{var g=document.createElement("ins");g.className="adsbygoogle";g.style.display="inline";if(rtbW>=960){g.style.width="580px";g.style.height="400px";g.setAttribute("data-ad-slot","9935184599");}else{g.style.width="300px";g.style.height="600px";g.setAttribute("data-ad-slot","9935184599");} g.setAttribute("data-ad-client","ca-pub-1812626643144578");g.setAttribute("data-alternate-ad-url",stroke2);document.getElementById("yandex_rtb_4").appendChild(g);(adsbygoogle=window.adsbygoogle||[]).push({});}})});
window.addEventListener("load",()=>{
var ins=document.getElementById("yandex_rtb_4");if(ins.clientHeight =="0"){ins.innerHTML=stroke3;}},true);
Ниже приведен перечень способов визуализировать состояние рабочего места.
Первый шаг 5S
красные метки на запасах
красные метки на оборудовании
красные метки на рабочих участках
карты канбан
Второй шаг 5S
Третий шаг 5S
Четверный шаг 5S
чек-лист состояния удаления ненужного
чек-лист состояния рационального размещения
чек-лист состояния уборки
Пятый шаг 5S
Ссылки приведут вас к более пространным описаниям, сдесь же отмечу следущиее: визуализация, как метод управления, облегчает понимание текущей ситуации: когда, где и что происходит или вот-вот произойдет. Визуализация помогает ускорить процесс приинятия решения. Скажем, если о срыве производства партии продукции можно узнать только в конце рабочего дня, это как минимум грозит задержкой отгрузки продукции на сутки. Если же в течение рабочего дня, пользуясь теми или иными методами визуального контроля менеджер видит, что “если мы будем работать в том же духе, то заказ будет сорван”, то у него есть возможность значительно раньше принять решение, что теперь с этим делать.
Фото взято из этой видеозаписи (к сожалению, только на английском языке), которая рассказывает еще об одном методе управления бережливым производством, который используется в компании FastCap.
Кому это может быть интересно
Узнать, кто эти люди…
Визуальное управление в бережливом производстве
Сущность и значение визуального управления
Применение визуального управления в системе бережливого производства дает возможность достичь следующие 2 важные цели:
- непрерывно владеть ситуацией на рабочем месте, наблюдать за происходящим и сделать проблемы наглядными, видимыми
- сделать гораздо более ясными задачи по улучшению (например, установить визуальные целевые показатели, сделав, при этом, видимыми как цели, так и текущие результаты)
if(rtbW>=960){var rtbBlockID="R-A-744041-3";} else{var rtbBlockID="R-A-744041-5";}
window.yaContextCb.push(()=>{Ya.Context.AdvManager.render({renderTo:"yandex_rtb_3",blockId:rtbBlockID,pageNumber:3,onError:(data)=>{var g=document.createElement("ins");g.className="adsbygoogle";g.style.display="inline";if(rtbW>=960){g.style.width="580px";g.style.height="400px";g.setAttribute("data-ad-slot","9935184599");}else{g.style.width="300px";g.style.height="600px";g.setAttribute("data-ad-slot","9935184599");} g.setAttribute("data-ad-client","ca-pub-1812626643144578");g.setAttribute("data-alternate-ad-url",stroke2);document.getElementById("yandex_rtb_3").appendChild(g);(adsbygoogle=window.adsbygoogle||[]).push({});}})});
window.addEventListener("load",()=>{
var ins=document.getElementById("yandex_rtb_3");if(ins.clientHeight =="0"){ins.innerHTML=stroke3;}},true);
В контексте системы бережливого производства визуальное управление можно осуществлять следующими 3 способами:
- при помощи индикаторов (ключевых показателей)
- с помощью фото
- при помощи разметки.
Индикаторы в визуальном управлении
Замечание 1
Они представляют собой таблицу или график, на которых иллюстрируются заданные и фактические значения показателей (таких как, в частности: количество ошибок, выработка и т. д.). Ключевые показатели (или индикаторы) обычно размещают на информационных досках, находящихся обычно на каждом из участков.
В самом начале смены менеджер может собрать всех работников на несколько минут, для того чтобы обратить их внимание на достигнутые за прошлую смену значения показателей (результаты) по каждому из сотрудников. При этом, делается акцент на причинах успеха тех, кто продемонстрировал наилучшие результаты. Обязательно также выясняются причины неудач работников, показавших невысокие результаты (а точнее – результата, которые ниже ожидаемых). Непременно даются рекомендации по использованию передового опыта, а также по следованию имеющимся стандартам. По окончании смены дается несколько минут для приведения рабочего места в порядок . За это время менеджер на информационной доске отмечает достигнутые за смену результаты.
Готовые работы на аналогичную тему
Фотографии, разметка
Довольно простым решением для эффективной визуализации является фото рабочего места, стеллажа и т. д. Так, к примеру, если в офисном шкафу папки расположены стандартизовано (и, при этом, имеется фото «идеального варианта»), то отсутствие какой-нибудь из папок тут же окажется заметным. Наличие полоски на каждой папке дает возможность разместить их в необходимом и оптимальном порядке.
Разметка предназначена для того, чтобы видеть то, как должны перемещаться материальные потоки, где должно находиться оборудование и т.д. Четко отмеченные и разграниченные места (к примеру, для тележек или ящиков на складе) дают возможность не расходовать время на постоянный их поиск.
Во многих фирмах для классификации уже упакованного товара и для последующей отгрузки по разным точкам применяется цветной скотч (его применение в производственном процессе также можно смело отнести к категории «визуальное управление»).
Информационная доска
При размещении сведений на доске необходимо стараться избежать лишней информации. Это далеко не всегда является простой задачей, потому как в большинстве случаев информация довольно разнообразна), но все же, необходимо стараться отображать лишь ту, которая наиболее необходима на данном участке, например:
- показатели исполнения (результаты работы за определенный период, в количественном выражении), которые служат основой для периодического собрания работников
- показатели производительности (проблемы качества, фактическая выработка по сравнению с плановой и т.д.; подобного рода информация, в основном, служит основой для ежедневной «пятиминутки»
- общая информация (объявления, распоряжения и т.д.).
if(rtbW>=960){var rtbBlockID="R-A-744041-3";} else{var rtbBlockID="R-A-744041-5";}
window.yaContextCb.push(()=>{Ya.Context.AdvManager.render({renderTo:"yandex_rtb_2",blockId:rtbBlockID,pageNumber:2,onError:(data)=>{var g=document.createElement("ins");g.className="adsbygoogle";g.style.display="inline";if(rtbW>=960){g.style.width="580px";g.style.height="400px";g.setAttribute("data-ad-slot","9935184599");}else{g.style.width="300px";g.style.height="600px";g.setAttribute("data-ad-slot","9935184599");} g.setAttribute("data-ad-client","ca-pub-1812626643144578");g.setAttribute("data-alternate-ad-url",stroke2);document.getElementById("yandex_rtb_2").appendChild(g);(adsbygoogle=window.adsbygoogle||[]).push({});}})});
window.addEventListener("load",()=>{
var ins=document.getElementById("yandex_rtb_2");if(ins.clientHeight =="0"){ins.innerHTML=stroke3;}},true);
Замечание 2
Всегда следует стараться отсеивать ненужную и неактуальную информацию, а также не перегружать ее изобилием показателей. Сама же информация должна быть размещена в наиболее легкодоступных местах и быть понятной без излишних разъяснений и комментариев.
Визуальный менеджмент в бережливом производстве
Сущность визуального менеджмента
Определение 1
Визуальный менеджмент представляет собой четкое описание стандартов, условий и целей работы на местах, которое служит для сравнения каждым работником фактического состояния дел и требований к эффективности производства.
С помощью визуального менеджмента проводят мероприятия, которые направлены на то, чтобы привести продукт в соответствие с заданными требованиями.
В общем понимании под визуальным менеджментом понимается совокупность методов и информации, которые поддерживают работников в процессе выполнения ими работы и обеспечивают обратную связь.
Формы визуального менеджмента
- Вывешивание пограничных образцов и стандартов. Так, хорошие и плохие детали выставляются на рабочем месте и сопровождаются комментариями о причинах отнесения того или иного образца к хорошему или плохому. Особенное внимание уделяется деталям, которые являются пограничными случаями.
- Сигнал Stoр/Go. Это может быть любая форма визуального и/или акустического сигнала, который дает информацию в части состояния процесса (лампа «тревожной» сигнализации, сирены и т.п.)
- Система Andon – это световое табло или система проводников, которые позволяют четко установить вид и место проблемной ситуации. Эта система поддерживает сотрудника тогда, когда ему требуется помощь во время выполнения того или иного процесса. Подобные системы применяются крупнейшими корпорациями для автоматической остановки процесса тогда, когда оперативно решить проблему нельзя.
- Автоматический стопор в автоматизированной установке, останавливающий производственный процесс в случае аварийной ситуации. Этот способ помогает предотвратить производство дефектных изделий, производственный цикл при этом возобновляется только после анализа и устранения проблемы.
if(rtbW>=960){var rtbBlockID="R-A-744041-3";} else{var rtbBlockID="R-A-744041-5";}
window.yaContextCb.push(()=>{Ya.Context.AdvManager.render({renderTo:"yandex_rtb_1",blockId:rtbBlockID,pageNumber:1,onError:(data)=>{var g=document.createElement("ins");g.className="adsbygoogle";g.style.display="inline";if(rtbW>=960){g.style.width="580px";g.style.height="400px";g.setAttribute("data-ad-slot","9935184599");}else{g.style.width="300px";g.style.height="600px";g.setAttribute("data-ad-slot","9935184599");} g.setAttribute("data-ad-client","ca-pub-1812626643144578");g.setAttribute("data-alternate-ad-url",stroke2);document.getElementById("yandex_rtb_1").appendChild(g);(adsbygoogle=window.adsbygoogle||[]).push({});}})});
window.addEventListener("load",()=>{
var ins=document.getElementById("yandex_rtb_1");if(ins.clientHeight =="0"){ins.innerHTML=stroke3;}},true);
Готовые работы на аналогичную тему
Замечание 1
Вывешиваемая информация должна касаться только специфических мест или процессов, нет смысла вывешивать ту информацию, которая несет общий характер и затрагивает работу предприятия в целом.
При этом только вывесить информацию недостаточно, каждому сотруднику следует понимать, что эти сведения – часть его должностных обязанностей, которая позволит улучшить рабочий процесс.
Замечание 2
С помощью подобных визуальных устройств традиционное производство становится бережливым производством.
Визуальный менеджмент — ключевая сила совершенствования и гарантия того, условия бережливого производства являются ясно читаемыми, понятными, и их придерживаются постоянно.
Первичной причиной неэффективных затрат является дефицит информации из-за того, что персонал просто испытывает недостаток в знаниях о способах повышения эффективности их рабочих мест. С помощью визуального менеджмента можно существенно улучшить производительность, качество, удовлетворенность клиента, безопасность и т. д.
Инструментарий визуального менеджмента
Среди основных инструментов, которые могут быть использованы в визуальном менеджменте, можно назвать следующие:
- видеозапись происшествий,
- разработка визуальных стандартов,
- визуализация анализа проблемы (с помощью диаграммы Парето, «рыбьей кости» и т.п.),
- визуализация базовых показателей рабочих мест,
- схема перекрестного обучения,
- визуализация показателей деятельности всего предприятия.
Этапы внедрения визуального менеджмента
Внедрение визуального менеджмента предполагает последовательное прохождения ряда этапов:
- Первый этап посвящен организации рабочих мест.
- Затем, во время второго этапа визуализируется ключевая информация, которая расположена на рабочем месте: информация относительно безопасности, качества, последовательности выполнения операций и правилах эксплуатации оборудования.
- В рамках третьего этапа визуализируются показатели эффективности и результаты различных процессов.
- На четвертом этапе на базе данной визуализированной информации принимаются решения в части визуального менеджмента.
Системы визуального контроля совершенствуют поток создания добавленной ценности
Системы визуального контроля совершенствуют поток создания добавленной ценности
Визуальный контроль включает любые средства коммуникации, используемые на производстве, которые позволяют с первого взгляда понять, как должна выполняться работа и есть ли отклонения от стандарта. Он помогает сотрудникам, которые стремятся выполнить свою работу хорошо, немедленно определить, как они с ней справляются. Он может предусматривать обозначение места, отведенного под какие-либо объекты, указание на число объектов, которые следует установить на это место, стандартные процедуры выполнения определенной работы, состояние незавершенного производства и другие виды информации, важной для потока работ. В самом широком смысле визуальный контроль представляет собой комплекс информации всех видов, предоставляемой по системе «точно вовремя», с целью быстрого и надлежащего осуществления операций и процессов. В повседневной жизни есть множество ярких примеров такого контроля, например дорожные знаки, вывески и таблички. Поскольку речь идет о жизни и смерти, дорожные знаки обычно являются отлично продуманным средством визуального контроля. Хорошие дорожные знаки не требуют длительного времени на изучение: их значение понятно сразу.
Визуальный контроль не ограничивается выявлением отклонений от цели или задачи и представлением таких сведений на всеобщее обозрение в виде карт и графиков. Визуальный контроль в Toyota тесно связан с работой по созданию добавленной стоимости. Визуализация означает, что вы можете взглянуть на процесс, единицу оборудования, запасы, информацию или рабочего, выполняющего свои обязанности, и сразу увидеть стандарт, который используется при выполнении данной задачи, и возможные отклонения от этого стандарта. Задайте себе такой вопрос: может ли руководитель, который идет по цеху, офису или предприятию, сразу определить, соблюдается ли стандартная рабочая процедура? Если у вас есть четкий стандарт, который определяет место для каждого инструмента, и этот стандарт представлен наглядно, тогда руководитель сразу увидит, что находится не на месте. Именно поэтому в рамках программы «5S» часто создаются стенды для инструментов. На отведенном для инструмента месте на стенде изображен его контур. Контур молотка показывает, где должен находиться молоток, и если его нет на месте, это видно сразу. Подобным образом наличие наглядных меток, которые показывают минимальный и максимальный уровень запасов, позволяет руководителю (и не только ему) увидеть, какова ситуация с запасами. Продуманные карты и графики, в которые вносятся ежедневные поправки, позволяют контролировать ход выполнения проектов в офисах.
Принцип 7 подхода Toyota требует использования визуального контроля для совершенствования потока. Отклонения от стандарта при наличии потока единичных изделий приводят к отклонениям от времени такта. На деле многие инструменты, связанные с бережливым производством, представляют собой средства визуального контроля, используемые для выявления отклонений от стандарта и обеспечивающие бесперебойный поток. Примерами таких инструментов являются канбан (ячейка, работающая по принципу потока единичных изделий), андон и стандартные операции. Если на контейнере нет карточки канбан, которая требует наполнить его, значит, контейнер не на месте. Наполненный контейнер без карточки канбан – это визуальный сигнал перепроизводства. Продуманная ячейка позволяет немедленно обнаружить лишние единицы незавершенного производства благодаря тому, что места для стандартного запаса незавершенного производства соответствующим образом промаркированы. С помощью андон подается сигнал об отклонении от стандартных рабочих условий. Стандартная процедура выполнения задания вывешивается так, что можно сразу увидеть наилучший из известных методов обеспечения потока на каждом рабочем участке. Замеченные отклонения от стандартной процедуры свидетельствуют о наличии проблемы. В сущности, Toyota использует единый комплекс средств визуального контроля, или систему визуального контроля, которая обеспечивает прозрачность рабочей среды, где потери сведены к минимуму. Давайте посмотрим, как визуальный контроль способствует совершенствованию потока на огромном «бережливом» складе, где такая возможность кажется особенно неправдоподобной.
Данный текст является ознакомительным фрагментом.
Читать книгу целиком
Поделитесь на страничке
Следующая глава >
|
Визуальный контроль в «бережливом производстве»
Одной из главных задач концепции «бережливого производства» является непрерывное устранение потерь. Рассмотрим некоторые идеи реализации этого подхода с точки зрения внедрения систем технического зрения Omron.
Перепроизводство.
Производство продукции «на склад» и связанные с обслуживанием и хранением операции являются потерями, не несущими ценности для потребителя. Для решения этой проблемы «бережливое производство» предлагает производить продукцию точно под заказ или минимальными партиями. Эту систему называют «Just-in-time».
Контроль качества динамично меняющихся видов продукции осложнен для человека. Возникает риск возникновения других потерь: предпосылки к выпуску продукции с отклонениями, возрастанию потерь времени на переналадку оборудования.
Системы технического зрения хранят настройки для очень большого числа задач и моментально переключаются на другой вид продукции или задачу. В арсенале контроллера FH более 100 инструментов анализа изображений и 128 оперативно хранимых сценариев настройки, что делает его очень универсальным средством.
Предотвращение ошибочных действий.
«POKA-YOKE» или «Защита от дурака» — методика исключения неправильных действий.
Идентификация продукции в процессе сборки, выполняемая тех. зрением может создавать инструкции для сборщика, подсказывающие или разрешающие соблюдение требуемой последовательности и комплектации изделия.
Контроль перед финальной операцией сборки. Операция контролирует правильность сборки и полную комплектность изделия перед финальной операцией, исключающей изготовление бракованного изделия.
Еще один момент — избыточность интерфейсов систем управления. При необходимости создания интерактивного воздействия оператором на процесс визуального контроля, с системой технического зрения Omron пользовательский интерфейс может быть индивидуально приспособлен под конкретную задачу. Делается это путём свободного выбора места размещения элементов интерфейса, а ненужные элементы могут быть скрыты. Программное обеспечение позволяет иметь различные виды интерфейса для разработчика и конечного пользователя.
Снижение допустимых отклонений.
Автоматизированный визуальный контроль способен сделать новый шаг в воздействии на причину возникновения отклонений качества продукции. Анализ с помощью технического зрения дает возможность произвести детальные и количественные измерения отклонений. И что, также важно, делать это непрерывно, накапливая статистику. Техническое зрение может сохранять результаты анализа и непосредственно изображения инспектируемых изделий. Порой, только анализ таких данных дает возможность понять причину отклонений и исследовать качество влияния корректирующих воздействий. Результатом может быть достижение качества изделий выше необходимых требований.
1. Систематический анализ процесса
2. Корректировка
3. Уменьшение рассеивания
Отслеживание перемещения продукции в цикле производства.
Для сбора и сохранения информации о процессе производства продукта в пределах всего производственного цикла, – от сырья (или исходных комплектующих) до склада готовой продукции, применяются технологии прослеживаемости продукта. А для некоторых продуктов, прослеживаемость может выходить и за рамки производственного процесса, помогая предпринять действия, направленные на улучшение качества изделий, находящихся уже в эксплуатации. Такое отслеживание проводится путем присвоения и контроля серийных номеров изделий. В большинстве случаев маркировка осуществляется штрих-кодами.
Коммуникационные возможности систем Omron на основе стандартных интерфейсов позволяют встраивать их в распределенные системы. Камеры умеют считывать все наиболее используемые штрих-коды, а также распознавать текст, если маркировка нанесена в виде, предназначенном для чтения человеком.
Идея непрерывного улучшения и модернизации лежит в основе философии «бережливого производства». И перед тем, как сделать первый шаг и начать, даже, маленький проект, который сегодня что-то улучшит в технологической цепочке, нужно принять во внимание некоторые идеи, как это решение может развиваться в будущем.
Решение, которое отвечает идее постоянного улучшения должно быть:
Масштабируемое:
- Начиная с одного продукта, оно может быть применимо ко всем продуктам.
- От одной линии, до других линий и производственных площадок.
Интегрируемое:
- В создаваемую систему должны легко интегрироваться новые элементы.
- Последующее использование наработок снижает затраты на новые разработки.
Обслуживаемое:
- Минимальное время поиска неисправностей и переналадки.
Легко применимое:
- Использование должно быть простым для всех подразделений и новых пользователей.
- Унификация настройки оборудования.
Линейки технического зрения Omron разработаны как модульная система с гибкими возможностями. Для коммуникации используются стандартные интерфейсы и протоколы, облегчающие интеграцию с различным оборудованием.
Контроллеры серии FH комбинируются с очень широкой линейкой камер: от 0.3 МП до 12 МП и большим количеством вариантов объективов.
Возможность высокоскоростной обработки изображений с высоким разрешением обеспечена благодаря оснащению контроллеров мощными многоядерными процессорами. Но, в то же время, сохранена гибкость выбора оптимальной цены за счет наличия в линейке модели FH-Lite.
Системы технического зрения разработаны, как продукт, входящий в единую «экосистему» решений Омрон. Где программирование и настройка оборудования осуществляются в единой программной среде, обеспечивая прозрачность, переносимость настроек и легкую совместимость.
Информационная коллекция обучающих ссылок Lean и Sigma Six
Бережливое производство
Бережливое производство — это, по сути, система непрерывного или повторяющегося совершенствования, посредством которой человек постоянно улучшает или пытается улучшить способы выполнения конкретной задачи или работы. Это система непрерывного улучшения качества, процессов, технологий, производительности, безопасности, корпоративной культуры, характеристик и отношения рабочей силы, а также лидерства. Бережливое производство как система было разработано в Японии после Второй мировой войны и теперь используется во всем мире
В основе бережливого производства лежит улучшение каждой области вашего бизнеса путем постоянного стремления делать вещи более эффективно и без ошибок.
Базовых арендаторов Бережливого производства несколько:
- Кайдзен — одна из основных философий бережливого производства. На японском языке «Кай» означает исправлять, исправлять, улучшать или изменять, , а слово «дзен» означает хорошо, . Это основа философии постоянного совершенствования. Это не «процесс», который выполняется через регулярные промежутки времени — вместо этого он выполняется на постоянной основе.
- 5S — это системный подход к организации рабочего места.Это пятиступенчатый процесс, который способствует повышению эффективности, конкурентоспособности и выживания вашей компании.
- 6S развивает систему 5S и идет еще дальше. Все шаги в 5S важны, но есть еще одна важная буква «S»: безопасность.
- Six Sigma — это процесс, используемый для улучшения общего качества выпускаемой продукции. Он разработан для уменьшения причин отклонений и дефектов в производимой продукции, и для его функционирования он полагается на несколько других процессов управления качеством.
- Zero Defects — это еще одна философия бережливого производства, направленная на повышение качества, которое является основным ингредиентом успеха в любом бизнесе или производственной организации.
Сегодня в мире существует множество других методов и принципов бережливого производства. Для получения дополнительной информации о бережливом производстве у нас есть различные обучающие видео по бережливому производству и инструменты для бережливого производства, а также другие продукты 5S, которые могут оказаться полезными.
.
Visual Factory, гибкое программное обеспечение и постоянные встречи: принципы бережливого производства, часть 9
Visual Factory занимается улучшением коммуникации
Это часть 9 нашей серии статей о принципах бережливого производства.
Плохое общение — проклятие практически любой формы совместной работы. Чем сложнее процесс, над которым команда работает вместе, тем сложнее правильное общение, но также тем важнее становится его успешное выполнение.
Несколько своеобразное название этой статьи и включение в нее Agile Software и постоянных встреч, связано с тем, что идеи Visual Factory напоминают некоторые из ранних практик, которые я использовал для управления командами разработчиков программного обеспечения, чтобы улучшить их взаимодействие. Эти методы включали создание «Постоянного собрания», которое включало в себя краткое собрание всей моей команды каждый день, чтобы убедиться, что общение происходит. Некоторые авторитеты считают, что моя первоначальная команда Quattro Pro (да, я уже довольно давно занимаюсь тем или иным калькуляторами!) Начала эту важную часть методологии Agile Software.Я делал упор на том, что нового, что должно быть ясно, и на том, чтобы встречи были очень короткими: максимум от 15 минут до получаса. Они также были очень наглядными, когда это было возможно. Мы не хотели просто обойти стол и получить обычный скучный отчет о проделанной работе. Вместо этого мы по возможности настаивали на демонстрации новых функций и разработок.
Я не буду здесь особо вдаваться в подробности Agile Software, за исключением того, что быстрое 10-минутное совещание в начале каждой смены может быть очень полезным, чтобы убедиться, что каждый в команде точно знает, что им нужно сделать во время смены. .Заставить такие встречи работать — это искусство, требующее подготовки, но результаты того стоят. Если вы хотите узнать больше об гибкой разработке программного обеспечения, по крайней мере, с точки зрения того, как я это практикую, я недавно опубликовал статью в своем блоге о бизнес-стратегии, в которой рассказывается эта история.
Возвращаясь к Visual Factory, концепция бережливого производства заключается в том, что общение страдает от потерь (в основном, когда оно не происходит четко, четко и легко), и поэтому стоит «отклониться». Если вы можете сократить время и ресурсы, необходимые для общения, вы можете повысить производительность, и в этом весь смысл бережливого производства.
В Visual Factory особое внимание уделяется визуальной коммуникации, поскольку она имеет ряд преимуществ:
— Быстро усваивается: картинка лучше 1000 слов. Сколько времени у вас уйдет на то, чтобы прочитать 1000 слов, а не на картинку?
— Визуальные эффекты обычно компактны. Нам не нужен длинный фолиант, нам, возможно, нужна вывеска размером с плакат.
— Визуальные эффекты упрощаются. В большинстве случаев, когда мы пытаемся что-то передать визуально, нам приходится это упрощать.
— Визуальные эффекты резюмируют. Взглянув на Канбан-доску, вы можете сказать, насколько близка к завершению работа в целом, из-за веса карточек с одной или другой стороны.
Это не означает, что Visual Factory полагается исключительно на чисто визуальные коммуникации без слов, просто он пытается быть незамедлительным, простым и доступным в любое время. Картинки могут помочь, когда для объяснения потребуется слишком много слов. Информация должна быть представлена в том месте, где она может принести наибольшую пользу.Это сокращает затраты на поиск или получение информации.
Типы информации, которые обычно обрабатываются Visual Factory, включают:
— Метрики процесса
— Этапы процесса
— Общая информация по использованию
Давайте подробнее рассмотрим каждый тип.
Метрики процесса
Process Metrics сообщает нам, идем мы по плану или по прогнозу. Они говорят нам, оправдываем ли мы ожидания руководства.Они также говорят нам, работают ли наши программы по улучшению.
Process Metrics становятся значительно более эффективными, если их можно обновлять в реальном времени. Старые новости не вызывают восторга, но покажите нам самые свежие, и мы будем заинтересованы. Покажите нам тенденции, достигающие кульминации в последних, и мы часто будем даже больше заинтересованы.
Для показателей процесса можно использовать различные виды табло. Одна уловка, которую часто можно увидеть в Кремниевой долине, — это настроить проектор в стиле домашнего кинотеатра для отображения данных в реальном времени, генерируемых программным обеспечением.Информация проецируется на какое-нибудь видное место, например, у входа в комнату отдыха, где люди могут видеть ее, проходя мимо. Вот один такой пример от фирмы Кремниевой долины:
В проекторах и экранах хорошо то, что они управляются программным обеспечением, поэтому они могут быть гибкими и даже переключаться вперед и назад для отображения нескольких дисплеев. Область, в которой размещается такая информация, на языке Lean часто называют «Информационным центром».
Связанный индикатор называется «Андон».Андоны — это светящиеся вывески, которые используются, чтобы что-то сигнализировать:
— Машина не работает
— Обнаружен дефект
— Обнаружена проблема безопасности
Есть еще много всего. Andon позволяет легко увидеть из любого места в цехе, где требуется внимание.
Этапы процесса или рабочие инструкции
Наличие шагов, необходимых для отображения конкретного процесса в виде знака или удобного ламинированного контрольного списка, было бы еще одним хорошим примером Visual Factory.Существуют даже сложные системы, которые могут делать это с помощью программного обеспечения. Например, это делает система на основе канбана в G-Wizard ShopFloor.
Рассмотрите возможность добавления фотографий к этапам процесса, как это показано в системе GW ShopFloor Kanban. Для рабочих мест ваши установочные листы — это этапы процесса, поэтому добавьте фотографии, чтобы сделать их как можно более наглядными.
Существуют гибридные комбинации показателей процесса и шагов процесса. Например, на сборочной линии Jaguar используется система, в которой любой из рабочих может потянуть за шнур, чтобы подать сигнал о наличии проблемы.Когда это происходит, их руководитель группы приходит на помощь. Если они не могут быстро вернуть все в нужное русло, руководитель группы тянет шнур, который останавливает всю линию, пока ее не починят.
Общая информация по использованию
Любая часто используемая информация, которая может быть размещена в виде вывески, может быть полезной и легко доступной. Постарайтесь разместить эту информацию там, где она может принести наибольшую пользу.
Общая информация об использовании может быть широкой или конкретной. Например, предположим, что у вас есть датчик на воздушной линии.Попробуйте использовать такую наклейку, чтобы сразу было видно, какое давление должно быть:
Можно представить себе всевозможные визуальные индикаторы, подобные этому, для профилактического обслуживания и подобных целей. Купите таймер с подходящим интервалом времени и подключите его к цветному свету. Теперь у вас есть напоминание о том, когда пора проверять охлаждающую жидкость в машине или выполнять другую периодическую задачу. Как насчет этой изящной визуальной системы, чтобы определить, когда пора заказать еще кассету:
Заключение
Visual Factory — это использование визуальных методов для минимизации коммуникационных потерь.Чем проще и удобнее мы общаемся, тем больше шансов на успех!
Помогите нам!
Если вам понравилась эта статья, пожалуйста, передайте ее своим друзьям по электронной почте, разместив на своих любимых досках или нажав одну из наших кнопок ниже, чтобы «Твитнуть», «Мне нравится» и так далее. Мы действительно это ценим!
Присоединяйтесь к 100 000+ ЧПУ! Получайте наши последние сообщения в блоге бесплатно раз в неделю прямо на ваш почтовый ящик.Кроме того, мы предоставим вам доступ к отличным справочным материалам по ЧПУ, включая:
.
Бережливое производство | Операционный менеджмент и бизнес-стратегия
Кто мы?
Leanmanufacture.net — это веб-ресурс и веб-сайт в стиле блога, где вы можете узнать больше о бережливом производстве.
производство, управление операциями и бизнес-стратегия — от концепций и теории до реальных приложений, которые помогут вам достичь ваших производственных целей и задач.
Сайт
предназначен для удобства пользователя и представляет собой обширный ресурс знаний, который объясняет и решает фундаментальные проблемы успеха любого бизнеса для любого из студентов
предпринимателям, инженерам-технологам, менеджерам-консультантам и всем, кто интересуется этой широкой темой.Надеюсь, вам понравится этот сайт.
Бережливое производство Введение
Бережливое производство
или тощая
это производственный термин, используемый для описания производственной, промышленной или сервисной операции, которая работает с небольшим количеством или совсем без типа muda (отходы), что делает операцию очень эффективной и состоит только из шагов добавления стоимости от начала до конца, так как можно увидеть на карте потока создания ценности .Термин «бережливое производство» основан на идее о том, что покупатель, покупающий товар или услугу, готов платить только за «шаги» с добавленной стоимостью при создании или предоставлении такой услуги. Таким образом, не добавляющие ценность «шаги» и связанные с ними затраты покрываются производственной компанией, что снижает маржу для производителя. Многие концепции заимствованы из производственной системы Toyota, которая считается пионером в разработке нескольких концепций и принципов бережливого производства .
Производство пережило революцию в начале 20-го века, когда Генри Форд создал сборочную линию для массового производства Ford модели T.Даже тогда, когда до концепции бережливого производства остались годы, Ford сосредоточился на сокращении времени и отходов материалов, повышении качества и снижении циклов на , чтобы получить более дешевый автомобиль, что отразилось в снижении цены на модель T из года в год. Такой подход позволил ему сократить расходы, даже несмотря на то, что он хорошо платил своим работникам, и предоставить покупателю продукт с высокой стоимостью.
Позднее Toyota разработала модель Just in time (JIT) .
как мы знаем это сегодня.Модель нацелена на непрерывный поток материалов в процессе с
минимальные запасы или незавершенное производство (WIP) через различные рабочие места или этапы, добавляющие добавленную стоимость. JIT — это
система вытягивания, которая адаптируется к потребительскому спросу и обычно реализуется с помощью системы канбан . Подробнее о JIT можно прочитать в разделе JIT на этом веб-сайте.
В современном мире все больше и больше организаций осознают, насколько важно устранение бесполезных ресурсов, повышение качества и удовлетворенность клиентов для поддержания конкурентоспособного бизнеса.Также существует необходимость сократить производство, эксплуатацию и
затраты на инвентаризацию и повышение эффективности не только на производстве, но и в различных отраслях промышленности, таких как банковское дело, бизнес и общественные услуги.
Сегодня задача состоит в том, чтобы успешно адаптировать эти концепции и технологии к широкому спектру отраслей. Ключом к успеху в реализации принципов бережливого производства в любой организации является формирование культуры постоянного совершенствования в рамках ее корпоративной культуры , нацеленности на качество , бережливого мышления и удовлетворения потребностей клиентов как конечной цели организации.Этот сдвиг в культуре, если он еще не произошел, должен исходить от высшего руководства и быть воспринят всеми слоями организации.
& nbsp
& nbsp
.
Бережливое производство в эпоху промышленного Интернета
Транскрипция
1 Бережливое производство в эпоху промышленного Интернета От движущейся сборочной линии Генри Форда до производственной системы Toyota Тайити Оно, ныне известной как бережливое производство, производители во всем мире постоянно стремились улучшить свои операции.Концепция бережливого производства, широко известная своими инструментами для устранения процессов, не создающих добавленной стоимости, была в центре внимания менеджмента в течение последних пяти десятилетий. Бережливое производство позволило отдельным производителям преобразовать свою деятельность, сделав ее более эффективной, продуктивной, а их бизнес — более прибыльным. Будь то непосредственные работники, решающие сложные проблемы, улучшенное планирование с своевременным производством или остановка производственной линии, как только возникает проблема, бережливое производство заключается в внесении физических изменений для улучшения операций.
2 Это было тогда, это сейчас Представьте себе дискретную производственную среду, в которой ваши машины и устройства подключены, и люди имеют доступ к оперативной информации, где бы они ни находились, с бизнес-аналитикой на кончиках пальцев. Представьте себе производственный цех, где операционные данные преобразуются в интеллектуальное предвидение, чтобы сообщить работникам, например, где найти дополнительную эффективность в производстве, какие шаги предпринять для повышения урожайности и как и когда можно улучшить процессы для ускорения циклов.Похоже на сценарий на будущее? Фактически, достижения в области технологий делают это сегодня реальностью, позволяя бережливому производству приобретать более глубокий смысл, помимо улучшения простых процессов. Теперь производители могут использовать интеллектуальные данные, чтобы революционизировать свою деятельность и добиться значительных улучшений, включая повышение производительности, сокращение отходов и снижение затрат. Преимущества бережливого производства еще не реализованы в полной мере. Сегодняшние технологии, основанные на промышленном Интернете, позволяют предприятиям повышать ценность и выходить на новый уровень производительности, чтобы повысить свою конкурентоспособность.
3 Проблемы дискретного производства Производители дискретных устройств сталкиваются с растущими затратами, глобальной конкуренцией и растущим потребительским спросом. Они должны двигаться быстрее, лучше и стройнее каждый день, чтобы не отставать, не говоря уже о том, чтобы опережать конкурентов. Они вынуждены производить больше за меньшие деньги и быстро реагировать на меняющиеся требования рынка, одновременно снижая затраты.Короче говоря, производители должны учитывать все возможные операционные показатели. Таким образом, бережливое производство остается еще более важным, чем в прошлом. И чаще всего производители делают все возможное, чтобы максимально оптимизировать свои процессы. Ну что теперь?
4 Переход к бережливому производству на новый уровень Принципы «бережливого производства» — это принципы «шести сигм», которые также направлены на устранение потерь путем оптимизации и улучшения всех бизнес-процессов и устранения вариаций внутри процесса.Две дисциплины, бережливое производство и шесть сигм, могут быть особенно успешными при работе в тандеме — отсюда и термин «бережливое производство и шесть сигм». Но это не все. Возможность для производителей получить больше от бережливого производства «Шесть сигм» основана на стремительном росте объемов данных от современных подключенных к сети машин, обеспечиваемых промышленным Интернетом. Благодаря передовым решениям MES (система управления производством) эти данные могут предоставить своевременную и актуальную информацию, чтобы помочь улучшить как верхние, так и нижние показатели бизнеса, улучшая обслуживание клиентов, сокращая время выполнения заказа, улучшая производительность и эффективность операций, при этом избегая дорогостоящих ошибок. .Оцифровка производственных процессов и данных с помощью MES помогает выявить взаимосвязи и глубокое понимание в масштабах всего предприятия, чтобы стимулировать более эффективные и экономичные способы ведения бизнеса. Он обеспечивает основу, на которой аналитика больших данных может информировать о стратегическом планировании, управлять операциями в реальном времени и выявлять первопричины проблем, прежде чем они станут проблемами. Две дисциплины, бережливое производство и шесть сигм, могут быть особенно успешными при работе в тандеме — отсюда и термин «бережливое производство и шесть сигм».
5 Создание фундамента С точки зрения «бережливых» шести сигм, давайте рассмотрим, как использование программных технологий MES лучше всего подходит для поддержки этих инициатив.Для начала, есть несколько фундаментальных вопросов, на которые необходимо ответить, чтобы эффективно заложить основу: собираю ли я правильные данные? Есть ли у меня эффективный способ хранения и доступа к нему? Есть ли у меня способ визуализировать это в контексте? Есть ли у меня способ донести это до нужных людей? Как я могу интегрировать аналитику в свой производственный план?
6 GE Определите дорожную карту, которая будет ценить Вам необходимо определить желаемые результаты и расставить приоритеты для ваших целей.Например, ваши цели могут включать в себя одно или несколько из следующего: более быстрое производство продукции, сокращение незавершенного производства, усиление контроля за качеством, оптимизация цепочки поставок и снижение гарантийных расходов. Одновременное решение этих вопросов может оказаться непосильной задачей, поэтому вместо того, чтобы пытаться решить все, определите, какие из них наиболее эффективны для вашего бизнеса, а затем оптимизируйте их. Чтобы эффективно повлиять на эти желаемые результаты, сбор правильных данных является обязательным. Подумайте, какие значимые данные вам нужны о производственном процессе, критических активах и людях, и определите ключевые источники этих данных, будь то данные о продукте, данные об исполнении, рабочие инструкции, показатели качества, показатели цепочки поставок или данные генеалогии / прослеживаемости.Максимизируйте бережливое производство с использованием шести сигм с оцифровкой MES Определите дорожную карту ценности Каковы цели? Измерение производственных процессов Машины — Линии — Завод (а) Анализировать на основе данных Корреляции, производственный интеллект Стоит отметить, что промышленный Интернет позволяет производственной среде содержать данные не только внутри стен зданий, но также из источников и действий, которые служат предприятие (например, поставщики) и клиенты, которых обслуживают после того, как продукция покидает завод.Улучшение с помощью действенных данных В идеале данные, полученные от поставщиков (или ранее), встраиваются в производственные и сборочные операции, обеспечивая как анализ в реальном времени, так и целостное представление о важнейших действиях. Контроль для увеличения операционных расходов Нужные люди — мобильность Интеграция аналитики Производственный процесс
7 Измерение производственных процессов Следующим шагом является измерение производственных процессов с помощью возможностей, позволяющих собирать, хранить и управлять данными.Уровень необходимых данных будет определять, какая технология потребуется для сбора этих данных. Например, если вам нужны данные на уровне предприятия, которые масштабируются вместе с соответствующими производственными активами, может быть достаточно историка всего предприятия с возможностями моделирования данных и централизованного администрирования. Если вам нужно приблизиться к машине или производственному активу, например к датчику или системе управления, для которых требуется скорость сбора данных менее секунды, вы можете воспользоваться другим типом решения. Это может быть технология, которая позволяет встроить вычислительную мощность и возможность подключения в точку управления, создавая сеть интеллектуальных машин, подключенных к промышленному Интернету, для достижения желаемых показателей сбора.Вам также необходимо подумать о сборе данных на уровне предприятия, что может потребовать консолидации нескольких архиваторов предприятия в один архиватор с общей конфигурацией, чтобы обеспечить более оперативную аналитику и визуализацию. Наконец, дело не только в количестве или размере данных; это также о типе данных. Вам нужна способность обрабатывать несколько различных типов данных и соотносить их вместе в общем контексте. Например, это могут быть данные о продукте, данные о событиях и данные о качестве, которые имеют формат данных временных рядов, метаданных, изображений, видео и т. Д.все они должны управляться последовательным и последовательным образом, чтобы извлекать из этого пользу. Правильное решение MES позволяет собирать, хранить и управлять большими промышленными данными, являясь основой, на которой вы можете использовать аналитику более высокого уровня. Именно здесь бережливое производство по принципу «Шесть сигм» дает ценную информацию о бизнесе, и начинают проявляться значительные улучшения производительности. Уровень необходимых данных будет определять, какая технология потребуется для сбора этих данных.
8 Анализируйте на основе данных. Имея основание, производители могут использовать MES для построения аналитики разной степени, позволяющей решать очень конкретные проблемы их бизнеса.Например, такие решения могут анализировать наборы исторических данных и данных в реальном времени на предмет тенденций и закономерностей, а затем предупреждать соответствующий персонал о проблеме, требующей немедленного внимания, для поддержания и оптимизации производства. Решения MES играют критически важную роль, помогая операторам визуализировать данные и проводить основанный на данных анализ первопричин, чтобы определить, в чем заключалась проблема, что произошло, как часто это происходило, где это происходило и каким должно быть окончательное решение. Такой производственный интеллект может существенно повысить производительность и эффективность производственных операций, которые меняют правила игры.Анализ данных на основе расширенной аналитики помогает повысить производительность активов за счет обнаружения и прогнозирования того, почему, когда, где и как возникнут будущие потенциальные аномалии производства. Возможно, более важной является способность производителей оценить с помощью моделирования, какие потенциальные изменения в производственном процессе могут произойти, прежде чем они будут фактически реализованы. Например, крупный производитель дискретных продуктов использовал данные, собранные на производственном участке, несколькими различными способами. Исторические показатели процесса использовались, чтобы точно определить причину дефекта качества, обнаруженного во время окончательного тестирования продукта.Аналитика, примененная к данным, выявила разницу в рабочих процедурах между первой и второй сменами из-за того, что оператор слишком рано вынул продукт из критической операции. Эта основанная на данных информация позволила предпринять корректирующие действия для улучшения качества продукции. Этот же производитель смог выполнить моделирование производства на основе показателей производительности, собранных с течением времени. Он хотел понять последствия выхода из строя машины и какие рычаги она могла бы использовать, чтобы при этом производить продукцию в соответствии с графиками производства.Предварительное определение этих сценариев помогло компании определить потенциальные единичные точки отказа в производственном процессе и составить план действий на случай непредвиденных обстоятельств, позволяющий поддерживать производство в рабочем состоянии в случае сбоя. Превратите данные в полезные знания 1 3 Собирайте данные из ваших систем Предоставляйте релевантную информацию нужным людям 4 2 Преобразуйте данные в интеллектуальные идеи Повышайте эффективность работы с помощью бережливого производства
9 Расширенные возможности MES помогли производителю промышленных двигателей обеспечить экономичную работу, обеспечив лучшую прозрачность производственных операций.Предоставляя информацию в реальном времени и анализируя неэффективность, решение определило, что время настройки было слишком большим, и выявило основную причину, что позволило производителю решить проблему. Решение также определило время посадки; один предмет производился в другом здании, и доставка его до следующей операции могла занять два часа. Используя MES, производитель мог разослать запрос грузоотправителям, чтобы забрать НЗП и минимизировать время ожидания при следующей операции.Результаты: на 15% улучшено использование рабочей силы. На 15% уменьшено незавершенное производство и складские запасы сырья. Более быстрое время настройки и доставки. Оптимизация производства на основе наличия и материалов для своевременного выполнения заказов.
10 Улучшение с помощью данных, требующих принятия мер. Благодаря возможности измерения и анализа на месте ключевую роль играет подключение к данным нужных людей. Технологии визуализации MES обеспечивают оперативную аналитику в реальном времени, так что оператор, персонал диспетчерской, руководитель предприятия, инженер или обслуживающий персонал могут отделить сигнал от шума.Таким образом, он или она может расставить приоритеты в правильных действиях в нужное время. Соответствующая информация в контексте всегда под рукой, сотрудники могут идентифицировать критические части процесса и при необходимости углубляться в детали. Передача интеллектуальной информации нужным людям позволит производителям каждый раз принимать оптимальные меры, способствуя значительным операционным улучшениям. Более того, как и в потребительском мире, индустриальный мир становится все более мобильным, поэтому необходимо предпринять шаги, чтобы сделать данные доступными.Промышленная мобильность MES на базе промышленного Интернета позволяет современным производителям подключаться к своим производственным процессам из любого места в любое время на мобильных устройствах, что является мощным инструментом для ведения бизнеса. Мобильность также предоставляет руководителям доступ к информации в режиме реального времени, способствуя подходу к управлению на рабочем месте в отличие от подхода к управлению электронными таблицами. Эта практическая культура согласуется с философией бережливого производства и шести сигм, согласно которой информация и действия в реальном времени ускоряют инициативы по улучшению процессов.Соответствующая информация в контексте всегда под рукой, сотрудники могут идентифицировать критические части процесса и при необходимости углубляться в детали.
11 Контроль для повышения эффективности работы В конечном итоге вы хотите постоянно обеспечивать повышение эффективности работы на всем производственном предприятии. Поскольку промышленный Интернет обеспечивает связь между вашими машинами, данными, аналитическими данными и людьми, у вас есть инфраструктура, позволяющая использовать бизнес-аналитику и операционную информацию о будущем, превращая ваши операции в экономичнее, чем когда-либо.Чтобы поддерживать эти новые уровни экономичной производительности, MES позволяет интегрировать аналитику как часть вашего производственного плана, чтобы вы могли постоянно добиваться лучших результатов, таких как: глобальный производитель бытовой техники вводил в производство 10 новых наземных устройств параллельно на очень плотный график. Его существующие системы были разрозненными и не связанными друг с другом, им не хватало видимости и столь необходимой сквозной системы. Чтобы оптимизировать свои операции и обеспечить непрерывные улучшения, компания использовала мощное решение MES, которое предоставило интегрированную ERP-систему для производственной системы, точные и своевременные бизнес-показатели, полную генеалогию продуктов, визуализацию и контроль в реальном времени, а также оптимизацию расписания.Результаты: 6 Планируйте производство на заводах, линиях или машинах для производства в соответствии с установленными целевыми показателями 6 Сократите объем незавершенного производства за счет наглядности в режиме реального времени 6 Производите продукцию быстрее, замыкая цикл между производством и проектированием, чтобы быстрее доставлять продукцию клиентам 6 Повышение качества за счет сбора данных в режиме реального времени и показателей соответствия для проверки соответствия фактического исполнения заданному 6 Использование полной генеалогии продукта для быстрой прослеживаемости и сдерживания воздействия 6 Оптимизация производства на основе ограничений по энергопотреблению 6 Интеграция потребления энергии и воды в показатели управления материалами и потребления 30- Сокращение необработанных данных и незавершенных работ на 40%. Двузначное сокращение затрат на развертывание и скорости. Предполагаемое сокращение затрат на гарантийное обслуживание на 24% за счет сквозной генеалогии. Повышение качества и меньшее количество доработок. Увеличение времени безотказной работы на 20%.
12 Заключение Быстрый рост объемов данных, поступающих с подключенных сегодня компьютеров, благодаря промышленному Интернету, открывает перед производителями критическую возможность использовать решения MES для улучшения и экономичности ведения бизнеса.Промышленность стремительно движется к тому, чтобы аналитика была связана в точках контроля и процесса, так что производственные предприятия в конечном итоге будут самообучающимися, самосовершенствующимися и самообучающимися для повышения конкурентоспособности. Это мир, в котором мы живем, где технологии обеспечивают конвергенцию машинных и интеллектуальных данных, и все взаимосвязано. Чем раньше дискретные производители перейдут на оцифровку, тем быстрее они смогут использовать то, что для них могут сделать современные технологии.И тогда мощь промышленного Интернета становится реальной для производственных операций.
13 О компании GE GE предлагает промышленное программное обеспечение, системы управления и встраиваемые вычислительные платформы для оптимизации активов и оборудования наших клиентов. Наша цель — помочь нашим клиентам повысить прибыльность своего бизнеса с помощью высокопроизводительных решений для современного мира, связанного с сетями.Мы работаем в различных отраслях промышленности, включая энергетику, производство, водное хозяйство, горнодобывающую, нефтегазовую, оборонную и авиакосмическую промышленность. Мы являемся подразделением GE, со штаб-квартирой в Шарлоттсвилле, штат Вирджиния. Контактная информация GE Северная и Южная Америка: или Глобальные региональные номера телефонов указаны по местоположению на нашем веб-сайте GE, Inc. Все права защищены. * Торговая марка GE, Inc. Все остальные торговые марки и наименования являются собственностью их владельцев. Технические характеристики могут быть изменены без предварительного уведомления.
.