Стенд бережливое производство: ГОСТ Р 56907-2016 Бережливое производство. Визуализация, ГОСТ Р от 31 марта 2016 года №56907-2016 – Пошаговый план внедрения системы 5S – основополагающий инструмент бережливого производства | Алгоритм
if(rtbW>=960){var rtbBlockID="R-A-744041-3";} else{var rtbBlockID="R-A-744041-5";}
window.yaContextCb.push(()=>{Ya.Context.AdvManager.render({renderTo:"yandex_rtb_7",blockId:rtbBlockID,pageNumber:7,onError:(data)=>{var g=document.createElement("ins");g.className="adsbygoogle";g.style.display="inline";if(rtbW>=960){g.style.width="580px";g.style.height="400px";g.setAttribute("data-ad-slot","9935184599");}else{g.style.width="300px";g.style.height="600px";g.setAttribute("data-ad-slot","9935184599");} g.setAttribute("data-ad-client","ca-pub-1812626643144578");g.setAttribute("data-alternate-ad-url",stroke2);document.getElementById("yandex_rtb_7").appendChild(g);(adsbygoogle=window.adsbygoogle||[]).push({});}})});
window.addEventListener("load",()=>{
var ins=document.getElementById("yandex_rtb_7");if(ins.clientHeight =="0"){ins.innerHTML=stroke3;}},true);
13 уроков менеджмента от Procter and Gamble, дающих 100% качества и безопасности
if(rtbW>=960){var rtbBlockID="R-A-744041-3";} else{var rtbBlockID="R-A-744041-5";}
window.yaContextCb.push(()=>{Ya.Context.AdvManager.render({renderTo:"yandex_rtb_6",blockId:rtbBlockID,pageNumber:6,onError:(data)=>{var g=document.createElement("ins");g.className="adsbygoogle";g.style.display="inline";if(rtbW>=960){g.style.width="580px";g.style.height="400px";g.setAttribute("data-ad-slot","9935184599");}else{g.style.width="300px";g.style.height="600px";g.setAttribute("data-ad-slot","9935184599");} g.setAttribute("data-ad-client","ca-pub-1812626643144578");g.setAttribute("data-alternate-ad-url",stroke2);document.getElementById("yandex_rtb_6").appendChild(g);(adsbygoogle=window.adsbygoogle||[]).push({});}})});
window.addEventListener("load",()=>{
var ins=document.getElementById("yandex_rtb_6");if(ins.clientHeight =="0"){ins.innerHTML=stroke3;}},true);
Однажды я побывал на заводе P&G в Санкт-Петербурге. Перенимал успешный опыт компании по визуальному менеджменту производства (оперативному управлению производством). Дело было в уже далеком 2012 г.
Но и сейчас, в 2018 г. большинству российских производств еще очень далеко до этого уровня.
Итак, большой цех с десятками станков. Производят известные всем одноразовые бритвенные станки Gillette. В цехе чистота и порядок. Все зоны промаркированы.
Общий вид цеха производства бритвенных станков Gillette
Идешь и сразу понимаешь, где безопасно, а где — нет. На каждом участке стенд визуального менеджмента расположен. По-русски говоря, это доска с графиками и цифрами, показывающими степень выполнения плана, количество несчастных случаев и многое другое.
По словам работников, этот стенд ускорил процесс принятия оперативных решений в 3-4 раза, сделал производство прозрачным.
Теперь подробнее и с фотографиями.
1. Стенд «три в одном».
Общий вид стенда визуального менеджмента
2. У доски ежедневно проводятся планерки по 5-10 мин. Не «бла-бла-бла», а с фиксацией проблем. Вот в такой форме записывают проблемы. Сразу и решение предлагают и ответственного указывают.
Сюда фиксируются действия по результатам совещания
3. Существует система наставников на производстве. Наставники это рабочие с большим опытом, которые учат новичков. К ним можно обратиться за советом и помощью.
На стенде отмечается, кто из наставников за кем из рабочих закреплен. Все оборудование пронумеровано, есть краткое обозначение каждого станка. Красными или зелеными магнитами отмечается, работает оборудование или нет и сколько человек на нем работает.
if(rtbW>=960){var rtbBlockID="R-A-744041-3";} else{var rtbBlockID="R-A-744041-5";}
window.yaContextCb.push(()=>{Ya.Context.AdvManager.render({renderTo:"yandex_rtb_5",blockId:rtbBlockID,pageNumber:5,onError:(data)=>{var g=document.createElement("ins");g.className="adsbygoogle";g.style.display="inline";if(rtbW>=960){g.style.width="580px";g.style.height="400px";g.setAttribute("data-ad-slot","9935184599");}else{g.style.width="300px";g.style.height="600px";g.setAttribute("data-ad-slot","9935184599");} g.setAttribute("data-ad-client","ca-pub-1812626643144578");g.setAttribute("data-alternate-ad-url",stroke2);document.getElementById("yandex_rtb_5").appendChild(g);(adsbygoogle=window.adsbygoogle||[]).push({});}})});
window.addEventListener("load",()=>{
var ins=document.getElementById("yandex_rtb_5");if(ins.clientHeight =="0"){ins.innerHTML=stroke3;}},true);
Данные о работе оборудования и наставниках
4. Часть стенда посвящена уровню эффективности оборудования. Здесь указывают целевой уровень общей эффективности оборудования, ее план и факт. В комментариях пишут причины, почему не удалось достичь планового показателя.
Если вы забыли, как считать общую эффективность своего оборудования, прочитайте статью «3 показателя, которые ВЗОРВУТ эффективность вашего производства».
Мониторинг эффективности работы оборудования
5. Ежедневно отмечают количество несчастных случаев на «кресте безопасности» (зеленый цвет — отсутствие). Чем больше зеленого, тем лучше. Если весь крест будет зеленым, то даже издали будет видно, что на участке с безопасностью полный порядок.
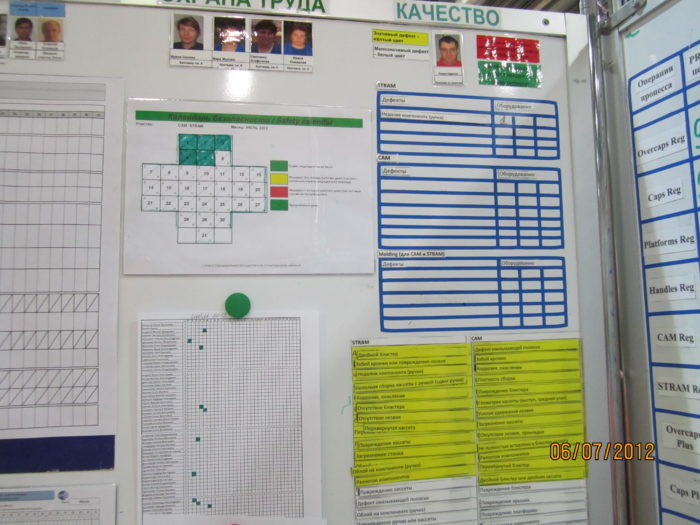
Данные о безопасности и проблемах с качеством
6. Существуют тонкие полоски из магнитной бумаги, на которых указаны типичные проблемы с качеством. При возникновении такой причины, полоска с нею крепится в специальном поле стенда. Там же указывается, на каком оборудовании возникла эта проблема. Ремонтные службы и контролеры, проверяющие стенд, оперативно реагируют на указанную проблему и устраняют ее. Искать их и жаловаться теперь не нужно!
Так фиксируются причины брака бритвенных станков
7. Существует стандарт по уборке и смазке каждой единицы оборудования. Часть его выполняет оператор оборудования, а часть — механик. На стенде ежедневно отмечается степень выполнения стандарта на каждой единице оборудования.
if(rtbW>=960){var rtbBlockID="R-A-744041-3";} else{var rtbBlockID="R-A-744041-5";}
window.yaContextCb.push(()=>{Ya.Context.AdvManager.render({renderTo:"yandex_rtb_4",blockId:rtbBlockID,pageNumber:4,onError:(data)=>{var g=document.createElement("ins");g.className="adsbygoogle";g.style.display="inline";if(rtbW>=960){g.style.width="580px";g.style.height="400px";g.setAttribute("data-ad-slot","9935184599");}else{g.style.width="300px";g.style.height="600px";g.setAttribute("data-ad-slot","9935184599");} g.setAttribute("data-ad-client","ca-pub-1812626643144578");g.setAttribute("data-alternate-ad-url",stroke2);document.getElementById("yandex_rtb_4").appendChild(g);(adsbygoogle=window.adsbygoogle||[]).push({});}})});
window.addEventListener("load",()=>{
var ins=document.getElementById("yandex_rtb_4");if(ins.clientHeight =="0"){ins.innerHTML=stroke3;}},true);
Данные о соблюдении стандартов обслуживания
8. Куда же на бережливом предприятии без 5С? Здесь, на Проктере система называется 6S. Это 5С с дополнительным шестым шагом, благодаря которому выполнение первых 5 шагов становится ежедневной привычкой работника. На отдельном листе отмечаются ответственные за содержание рабочих зон в чистоте и порядке и за соблюдение стандартов.
Мониторинг состояния рабочих мест по 6S
9. Есть проблемы и предложения? Записываем в отдельном месте.
Место для записи проблем и предложений
10. Точечный урок (one point lesson). Одностраничный урок — ситуация с двумя фото или схемой, нарисованной вручную. Цель — показать, как «нужно делать» и как «не нужно делать» какую-то конкретную операцию, работу и т.п. Краткий и простой стандарт.
Пример одностраничного (точечного) урока
11. Существует и мини-справочник дефектов бритвенного станка с описанием каждого дефекта и причинами его возникновения. Размещен здесь же.
Мини-справочник дефектов продукции
12. Есть простая схема станка с указанием названия основных узлов и ответственными за их обслуживание. Поломалось что-то — посмотрел сюда. И стало понятно, как называется «эта штуковина» и к кому обращаться за помощью.
if(rtbW>=960){var rtbBlockID="R-A-744041-3";} else{var rtbBlockID="R-A-744041-5";}
window.yaContextCb.push(()=>{Ya.Context.AdvManager.render({renderTo:"yandex_rtb_3",blockId:rtbBlockID,pageNumber:3,onError:(data)=>{var g=document.createElement("ins");g.className="adsbygoogle";g.style.display="inline";if(rtbW>=960){g.style.width="580px";g.style.height="400px";g.setAttribute("data-ad-slot","9935184599");}else{g.style.width="300px";g.style.height="600px";g.setAttribute("data-ad-slot","9935184599");} g.setAttribute("data-ad-client","ca-pub-1812626643144578");g.setAttribute("data-alternate-ad-url",stroke2);document.getElementById("yandex_rtb_3").appendChild(g);(adsbygoogle=window.adsbygoogle||[]).push({});}})});
window.addEventListener("load",()=>{
var ins=document.getElementById("yandex_rtb_3");if(ins.clientHeight =="0"){ins.innerHTML=stroke3;}},true);
Схема станка и указатель ответственных за состояние оборудования
13. Цели каждого работника на участке ясны и понятны. Размещены на огромном стенде на стене. Производительность — более 85%, количество остановок станка за смену — не более 36 шт., время между двумя остановками станка — более 20 мин.
Производственные цели каждого работника участка
Надеюсь, показанный опыт будет вам полезен. И вы обязательно примените его! А ваш бизнес станет еще более бережливым!
Хотите получать подобные материалы в будущем? Думаете, как сделать ваш бизнес бережливым? Подписывайтесь на рассылку Кайдзен от Клуба директоров. Мы поможем!
7 лет опыта внедрения Кайдзен-проектов. Сертифицированный эксперт в области бережливого производства от немецкого института Lean Management Institut. Работал с ООО «ПК НЭВЗ», ООО «Крафт Фудс Рус», ООО «Свеза-Лес», ООО «ТБМ-Юг». Я оказываю консультации по внедрению Кайдзен.
Ответы на вопросы: Стандарт доски визуализации
Получил вот такой вопрос: «Нужны ли единые доски визуализации по Бережливому производству по SQDCM, в крупной компании, где несколько сотен производственных площадок? Внешние консультанты против единообразия. А как ориентироваться на площадках, где какие показатели (их расположение)? Никак не могу отстоять позицию стандарта на стенд визуализации.»
if(rtbW>=960){var rtbBlockID="R-A-744041-3";} else{var rtbBlockID="R-A-744041-5";}
window.yaContextCb.push(()=>{Ya.Context.AdvManager.render({renderTo:"yandex_rtb_2",blockId:rtbBlockID,pageNumber:2,onError:(data)=>{var g=document.createElement("ins");g.className="adsbygoogle";g.style.display="inline";if(rtbW>=960){g.style.width="580px";g.style.height="400px";g.setAttribute("data-ad-slot","9935184599");}else{g.style.width="300px";g.style.height="600px";g.setAttribute("data-ad-slot","9935184599");} g.setAttribute("data-ad-client","ca-pub-1812626643144578");g.setAttribute("data-alternate-ad-url",stroke2);document.getElementById("yandex_rtb_2").appendChild(g);(adsbygoogle=window.adsbygoogle||[]).push({});}})});
window.addEventListener("load",()=>{
var ins=document.getElementById("yandex_rtb_2");if(ins.clientHeight =="0"){ins.innerHTML=stroke3;}},true);
Что могу сказать на эту тему.
Есть две заинтересованные в работе досок визуализации силы, интересы которых надо, по хорошему, уравновесить, чтобы «и волки сыты, и овцы целы».
Первая сила — это корпоративный менеджмент, который ставит задачу «чтобы везде работали доски визуализации и чтобы мы в любой момент могли увидеть текущее состояние дел в виде графиков/диаграмм/таблиц показателей в одном месте, чтобы не надо было бегать по всему заводу/цеху/участку». Если речь идёт об одной доске визуализации, то нет особой важности, как она выглядит, лишь бы всем было понятно, где на ней что находится, и лишь бы эта информация была актуальной и достоверной. Но если некоторые менеджеры вопреки вековым традициям начинают ходить по цехам/участкам, чтобы на месте увидеть все показатели и «на месте» же вмешаться в процесс, если того требует ситуация, то тогда возникает понятное желание «чтобы всё было одинаковое». Если стенды одинаковые, и набор информации на них расположен один и тот же в одном и том же виде, то нет необходимости искать на доске нужный тебе показатель — он всегда «в правом верхнем углу» находится, тут даже думать не надо.
Человеческий мозг не любит думать, на самом деле ему привычнее оперировать шаблонами. Те, кто ездят/ходят по одному и тому же маршруту, знают, что иногда ты начинаешь думать о настолько далеких от текущей ситуации вещах, что потом сложно вспомнить — а как именно ты сегодня ехал/шел и что по дороге видел. «На автопилоте прошел».
Именно исходя из этого мы стремимся везде использовать шаблоны, и менеджеры в этом ничем не отличаются от обычных людей.
Вторая сила — это сотрудники завода/цеха/участка, чью деятельность характеризует тот набор информации, который попадает на данный информационный стенд. Им нужно, чтобы «информация была достоверной, нужной именно для нас и удобной для использования нами, а не кем-то там еще». Почему? Потому что именно для этих сотрудников эта информация в первую очередь и нужна. И они должны работать с этим стендом значительно чаще, чем эпизодически приходящие менеджеры.
if(rtbW>=960){var rtbBlockID="R-A-744041-3";} else{var rtbBlockID="R-A-744041-5";}
window.yaContextCb.push(()=>{Ya.Context.AdvManager.render({renderTo:"yandex_rtb_1",blockId:rtbBlockID,pageNumber:1,onError:(data)=>{var g=document.createElement("ins");g.className="adsbygoogle";g.style.display="inline";if(rtbW>=960){g.style.width="580px";g.style.height="400px";g.setAttribute("data-ad-slot","9935184599");}else{g.style.width="300px";g.style.height="600px";g.setAttribute("data-ad-slot","9935184599");} g.setAttribute("data-ad-client","ca-pub-1812626643144578");g.setAttribute("data-alternate-ad-url",stroke2);document.getElementById("yandex_rtb_1").appendChild(g);(adsbygoogle=window.adsbygoogle||[]).push({});}})});
window.addEventListener("load",()=>{
var ins=document.getElementById("yandex_rtb_1");if(ins.clientHeight =="0"){ins.innerHTML=stroke3;}},true);
Будет ли мне интересно разглядывать на доске показатели, которые не относятся к моей работе? Не будет. Будет ли меня радовать тот факт, что 80% полезного пространства занимают данные, которые нужны не мне, а менеджеру, а, например, пространство для фиксации проблем, которые случились в течение смены, такое маленькое, что чтобы что-то там написать, нужно найти очень тонкий маркер и писать все слова с сокращениями, чтобы влезло? Это точно меня не будет радовать. Если вы хотите, чтобы я использовал визуализацию информации в своей работе, а не просто вешал листочки с графиками перед приходом высокого начальства, то дайте мне организовать информацию так, чтобы мне было удобно с ней работать, и чтобы это была значимая для меня информация, а не статистические данные о суточном потреблении риса на душу населения в Индии.
Если бы я строил свою компанию, по своим правилам, я бы запретил делать шаблонные доски визуализации, чтобы заставить менеджеров чаще выходить из статуса «автопилота» и чаще думать. Хотя бы в поисках ответа на вопрос «где, черт возьми, здесь эти данные?»
Но если я консультант, а не владелец, то я не буду это делать, потому что это не мои менеджеры, не я тут устанавливаю правила. Если они хотят чего-то шаблонного, это можно сделать, и при этом не слишком напрягать сотрудников, которые будут чаще пользоваться этими стендами визуализации.
Решение будет где-то посередине.
Что я имею в виду.
Всё пространство стенда визуализации (информационной доски) можно разделить на несколько зон, предназначенных для разных типов информации. Таких зон может быть 4, 6, 10, но не очень много, чтобы не перегружать избыточной информацией тех, кому она не нужна.
Какого рода информация будет отображаться в каждой зоне должно задавать шаблон. Например, во второй зоне — показатели, характеризующие качество продукции, в пятой — квалификацию персонала. Какие именно это будут показатели, в какой форме они будут изображаться — это определяет каждое структурное подразделение на свой вкус, в соответствии со своими потребностями. Нужно им 5 критериев качества в виде столбчатых диаграмм — пусть будет 5 столбчатых диаграмм. Нужен им только один критерий, но структурированный по видам дефектов — пусть там висит одна круговая диаграмма. Но качество — во второй зоне, а квалификация — в пятой.
Если дать еще чуть больше свободы, то размеры зон тоже можно позволить менять в каких-то пределах. Но их расположение должно оставаться одинаковым.
Тогда будет соблюдаться единообразие с точки зрения менеджеров, и при этом с точки зрения сотрудников подразделения не будет лишних органичений в том, как и какую информацию представлять на стенде.
Волки сыты? Да. Овцы целы? Да. Хорошо? Очень даже хорошо!
Небольшой пример про опасности излишней стандартизации. В одном проекте кто-то предложил поменять для 20 сотрудниц участка ножницы, чтобы «стандартизировать инструмент». А то у одной — большие, у другой — короткие. У одной — с закруглёнными кончиками, у другой — с острыми. Ножницы не были «основным инструментом», они не создавали основную ценность продукта, как было бы на участке раскроя тканей, или в парикмахерской. Тем не менее идею не реализовали. Оказалось, что каждой из 20 сотрудниц привычнее и удобнее работать теми ножницами, которые у нее были: у кого-то кисти рук крупные, у кого-то — поменьше, кому-то нужны ножницы с большими отверстиями для пальцев, а кому-то — нет. Кто-то привык острыми концами ножниц прокалывать скотч, чтобы надрывать его, а кто-то боится порезаться и пользуется ножницами с закруглёнными концами. На эффективность основной работы не влияет, так зачем менять? Чтобы красиво было?
Фото — с аудита участника конкурса на Кубок им. А.К. Гастева.
Кому это может быть интересно
Узнать, кто эти люди…
Бережливое производство «глазами» рабочего — LeanVector
Команда «Лин Вектора» в своей работе постоянно находится в диалоге в руководителями, специалистами и рабочими предприятий. Мы хотим обратить внимание на то, как воспринимается внедрение Бережливого производства рабочими.
Приводим в этой статье дословное интервью с работником одного из промышленных предприятий:
«Узнал я «Бережливом производстве» устроившись на одно из крупнейших предприятий нашего города. Работал на главном конвейере. Когда я устраивался, нам читали лекции о «Бережливом производстве» показывали примеры о том, как было и как стало. Рассказали о внедренных «Системе 5S» и «Кайдзен-предложениях». Мне это все показалось очень интересным.
Когда начал работать, «Бережливое производство» внедрялось уже полным ходом, все об этом говорят, размещены информационные стенды, на рабочих местах чисто, нет завала деталей. Одним словом – «Порядок». Понравилось, что руководители высшего звена проводят свои совещания, планерки прямо в цеху, на производстве. Для этих целей оборудовано специальное место.
Кайдзен-предложения, как я понял, были внедрены с целью сбора информации у рабочих по улучшению производственного процесса. С самого начала внедрения Производственной системы предприятия, Кайдзен-предложения были финансово мотивированы. С руководителей требовали Кайдзен-предложения, а они требовали с рабочих, даже был некий «план». Мы, рабочие, писали Кайдзен-предложения, получали пусть и небольшую надбавку к своей зарплате. Был виден результат этих предложений, но со временем финансирование уменьшилось и рабочие просто перестали «заморачиваться».
Отношение рабочих ко всему этому новшеству (внедрению Производственной системы) двоякое. Одни говорят, что стало намного лучше, чище, светлее, убрали завал деталей, уменьшились трудозатраты. У других отношение негативное — у них мнение, что это очередное отмывание денег. Третьим вообще безразлично. К сожалению, «сторонников изменений» меньше. В целом проблемы есть, но я бы сказал, что они возникают скорее от рабочей дисциплины, ответственности, как руководителей, так и рабочих.
Часто складывалось мнение, что делается «для галочки». К примеру, приходили проводить хронометраж. Ну пришли какие-то люди, даже не представились кто такие. О проблемах не спрашивали нас. Были не на всех позициях. Зачем приходили? Ничего после них не изменилось.
Другой пример – ввели процедуру, которая предусматривает остановку конвейера при возникновении проблем. Нам провел мастер инструктаж по этой системе. Но по факту процедура не соблюдалась — я не мог остановить конвейер, был «негласный запрет» несмотря на наличие кнопок останова…
По поставкам комплектующих – постоянные простои. Вроде заранее предупреждаю чтоб заранее подвезли. Но реакция часто была несвоевременной.
Со стороны некоторых мастеров чувствовалось безразличие. Мастеру часто было «не до улучшений».
Здесь читающему может показаться что было «все плохо». Но на самом деле было лучше, чем «раньше». Например, когда я ходил на соседние участки, на которых «бережливое производство» еще не было внедрено, была явно заметна разница. Сразу понимаешь, насколько у тебя чище, удобнее.
Поработав год на одном предприятии, я сменил место работы. Хочу сказать, что разница между предприятиями где внедрено «Бережливое Производство» и где его нет, весьма существенная.
Сразу бросается в глаза слабая культура производства, всюду производственный завал, неорганизованность. Я, как рабочий не понимал, для чего там нужны линейные руководители? Они очень слабо работают с подчиненными, нет взаимосвязи. Во время работы приходится делать очень много лишних действий из-за неорганизованности. Вечная проблема со средствами уборки на рабочих местах, с нехваткой того или иного.
Нет бережного отношения к оборудованию. Например, если рабочий видит, что скоро сломается какой-нибудь из элементов, то он все равно работает пока не произойдет поломка, а ведь это оборудование на котором он зарабатывает деньги.
Когда я пришел, молодой, энергичный, с небольшим опытом по «Бережливому Производству» то по просто по привычке наводил и поддерживал порядок на рабочем месте. На что люди, которые уже давно работают мне сказали: «Зачем ты это делаешь? За это не платят, и вообще из-за тебя нас всех заставят этим заниматься». Предлагая руководству какие-нибудь решения, по оптимизации рабочего процесса, удобству в работе, руководители попросту пропускали это все «мимо ушей». Чистоту и порядок наводят только перед проверкой, а не поддерживают постоянно. Как только у людей появляется свободное время, так они занимаются чем угодно, только не производственными делами. Как правило, берут свои телефоны и сидят в интернете, полностью отключаясь от реальности. Я вообще бы запретил интернет доступ для работников на рабочем месте, если его деятельность не связанна с ним.
Ведь работник, выполнив свою основную операцию сразу переключается на телефон, а ведь можно хотя бы прибраться. Часто встречал и вредительство со стороны работников, т.е. намеренную порчу оборудования, инвентаря и выпускаемой продукции. Это было связано с тем, что рабочие были недовольны условиями труда и отношениям руководства к себе («пофигизм»). Очень сильно проявляется это, когда рабочий увольняется и ему дают двухнедельную отработку. Вот здесь он начинает по настоящему «косячить»! Было ощущение, что руководители высшего звена совсем не знают и не понимают, что у них происходит на производстве. В общем, ощущение полного «хаоса»!
По своему опыту скажу, что «Бережливое Производство» для предприятия приносит очень большую пользу. Считаю ВАЖНЫМ донести до всех работников всю суть «Бережливого Производства»! ВАЖНО, что бы все работники осознали, для чего это делается и для чего это нужно! Независимо руководитель это или простой рабочий.»
Обращаем внимание на то, как воспринимается внедрение Бережливого производства рабочими. Очень часто приходится слышать от руководителей разного уровня, что «рабочим ничего не надо» и их «интересует только зарплата». По нашему опыту — это далеко не так. В основе мотивации любого человека лежит стремление к комфорту, социализация, признание («Пирадима Маслоу», 2,3,4 ступени). Соответсвенно, условия труда, коммуникации в компании важны для всех.
Основа Лин (Бережливого производства) — это система непрерывных улучшений (Кайдзен), которая позволяет вовлечь весь персонал в процессы улучшений. С этой позиции, степень вовлечения рабочих в процесс обозначения проблем, в процесс разработки и подачи предложений по улучшениям, будет индикатором развития Производственной системы.
Вам может быть интересна технология реализации проекта по развитию Бережливого производства.
1 вещь, которая сильно ускорит внедрение бережливого производства
Всё новое- это хорошо забытое старое. Поэтому я ничего нового не открою, но если у Вас всё вроде нормально, но чего-то не хватает, то этот кайдзен (улучшение) может здорово помочь.
Редко кто ориентируется в пространстве на слух или запах, поэтому самым естественным было бы в производстве использовать визуальное управление. Люди в большинстве своём визуалы. Принципы бережливого производства говорят, что непременно нужно применять визуальный менеджмент. Для его применения используется «Стенд визуального менеджмента» (СВМ).
«А-а-а Ну Я Это Знаю!», скажете Вы
Подождите, это присказка. Lean просто пронизан принципом прозрачности всего: прибыли, процессов, доходов, производства. Без этого просто невозможно видеть проблемы.
Для того, чтобы общаться и делать это эффективно внедряется так же 5-ти минутное совещание, которое проводится около СВМ.
На первых порах его проводит мастер, а потом постепенно инициатива переходит к бригадиру и далее к рабочим.
Почему и зачем?
Это создаёт команду, люди учатся говорить перед коллективом, а в России это далеко не каждый может- такое было Советское образование. Это происходит изо дня в день. Когда человек коммуникабелен- он может лучше найти решение проблем и объяснить потери в своей работе.
Что-то я отвлекаюсь. Объяснять ничего дальше не буду. Просто скажу, что «это работает» и «это проверено». Кайдзен – предложение заключается в том, чтобы использовать Указку при проведении совещания.
Казалось бы просто, Но нет!
Представьте себе ситуацию, когда ведущий совещание около стенда пытается довести до группы людей информацию, что индикатор качества бригады низкий. Что он делает? Показывает на индикатор. Чем? Пальцем (в лучшем случае- ручкой).
А теперь та же ситуация, но вся бригада собралась вокруг стенда для совещания. Мастер подходит, берет Указку, бригада затихает (это рефлекторно). Показывает Указкой на индикатор «Качество» и говорит: «Коллеги, качество нашей работы падает, а это плохо сказывается на авторитет участка. Что будем делать?»
Разница ощущается.
И еще одно замечание для lean – пятиминутки
Ведущий совещание должен держать указку в той же руке с какой стороны он стоит возле (не перед) стенда. Лучше- стоять справа и держать указку в правой руке.
Если научить мастера методически правильно проводить 5-ти минутное совещание, то ему обязательно понравиться. Хочу предостеречь от одного кайдзен, который некоторые могут захотеть применить. Указка должна быть именно физической. Не лазерная, не какая-то ещё, а именно предмет в форме «палка». Это важно.
Внедряя принципы бережливого производства многие полезные вещи, изученные раньше нанизываются на эту философскую систему, как на шампур и складываются в одно целое. И не знаешь, что на следующий день тебе пригодиться на этом интересном и полезном пути.
А насчет указки, так Вы просто попробуйте – что Вы теряете? А что получилось- пишите в комментариях.
Всегда Ваш, Игорь
доска задач, 5S, визуальная навигация — «Управление школой»
Прослушать статью
Тренд: бережливое производство
Подход «бережливое производство» сегодня внедряется во все сферы работы: промышленность, банковское дело, здравоохранение и т.д. Образование в этом ключе имеет много специфических особенностей, поскольку школы и детские сады сами по себе являются сложными организмами. Однако и здесь пригодятся универсальные, зарекомендовавшие себя подходы. Можно провести параллель между педагогическими методами/приемами и методами/инструментами бережливого производства. Подробнее с методами можно познакомиться в гостах:
- ГОСТ Р 12.4.026–2001 Система стандартов безопасности труда. Цвета сигнальные, знаки безопасности и разметка сигнальная. Назначение и правила применения. Общие технические требования и характеристики. Методы испытаний.
- ГОСТ Р 56020–2014 Бережливое производство. Основные положения и словарь.
- ГОСТ Р 56407–2015 Бережливое производство. Основные методы и инструменты.
Рассмотрим несколько известных инструментов бережливого управления.
Доска задач
Доска задач — это визуализация общего объема работы. Она позволяет определить уровень загруженности сотрудников и своевременно внести корректировки. Доска задач просто необходима, когда работа ведется сразу по нескольким направлениям и когда возможны внезапные существенные изменения в планах, новые срочные указания (например «спущенные сверху») — что актуально для любого образовательного учреждения.
Распространенные варианты «досок»:
- На магнитно-маркерной доске.
- На ватмане А1.
- На пробковой доске.
- В электронном виде.
Последний вариант, исходя из психологических особенностей людей, специалисты расценивают как наименее эффективный. Даже крупные it-компании часто использую именно доски из материалов, на которые можно физически прикреплять задачи и осязаемо выбрасывать их после выполнения.
Порядок определения задач зависит от размера штата и наличия различных подразделений. Представляем вам развернутый вариант работы с досками в организации:
Уровень рядовых сотрудников: в каждом структурном подразделении находятся доски со всеми задачами «на исполнении».
↓
Уровень заместителей директора: у каждого заместителя есть доска с 3-5 наиболее значимыми задачами по каждому сотруднику.
↓
Уровень директора: общая доска с 3-5 наиболее важными задачами по каждому подразделению.
Обычно «доски» делятся на два крупных блока: «В плане» и «В работе». На каждом стикере обозначается:
- Название
- Кто ответственен за выполнение
- Дедлайн
- % выполнения (он может зависеть от разных факторов: например, от качества или от соблюдения сроков).
Блок «В плане» содержит укрупненные задачи, которые нужно выполнить в ближайшие неделю-две. Например: «Проведение обучения для кураторов и тим-лидеров». Блок «В работе» — детализированные действия по каждой задаче. Например: «Направление информационного письма» или «Подготовка презентационных материалов».
На базе доски задач организовывать короткие ежедневные или еженедельные совещания на 10-15 минут, в формате руководство-подчиненные — чтобы определять перспективы дальнейшей работы. Доски задач можно и нужно использовать не только в решении педагогических вопросов, но и непосредственно при обучении детей (пример: технология «План — дело — анализ» в рамках популярной программы «Вдохновение» Лидии Свирской, доцента кафедры педагогики и психологии ОАОУ ДПО «Новгородский институт развития образования»). Уже в начальном обучении мы можем показать детям, как планировать свою деятельность и двигаться к достижению цели. Также имеет смысл посоветовать родителям внедрить доски задач в систему домашнего воспитания.
5S
5S — популярная система организации рабочего места, разработанная в послевоенной Японии. Она выстроена на основе пяти принципов: Сортировка, Самоорганизация, Систематическая уборка, Стандартизация, Совершенствование. Достигнем знаменитой японской собранности и лаконичности за 5 шагов:
Шаг 1. Сортировка (Сэири)
Делим вещи на нужные и ненужные, и испытываем удовольствие и разрядку, выбросив все ненужные вещи. Для этого делим инструменты, оборудование, материалы на 3 категории:
- Нужные всегда (то, что используем в данный момент).
- Нужные иногда (то, что периодически используем, но не в данный момент).
- Ненужные (то, что не используем, тара, посторонние предметы).
Ненужные предметы сразу выбрасываем (продаем, списываем, дарим). Увы, от некоторых вещей не так-то просто избавиться. Например, неизвестен хозяин вещи и его нужно найти, или есть большая вероятность, что она все-таки пригодится. В этих случаях используется инструмент «Кампания красных меток» — яркие ярлыки, которые постоянно напоминают о том, что пора решить судьбу неоднозначного предмета.
Шаг 2. Соблюдение порядка (Сэитон)
Делаем так, чтобы каждая вещь оказалась «на своем месте». Распределяя предметы по пространству, ориентируемся на принципы безопасности, качества вещей и их эффективность. Главные четыре правила расположения: на виду, легко взять, легко использовать, легко положить обратно. Клеим пиктограммы, поскольку с ними глазу проще ориентироваться в местах хранения оборудования и инвентаря, в рабочей зоне.
Виды пиктограмм и указателей:
- На местах хранения (какие предметы здесь должны находиться).
- На самих предметах (где этот предмет должен храниться).
- Количество (сколько предметов здесь можно разместить).
Помимо пиктограмм, разобраться в расположении предметов помогает контурирование: четкое обозначение места предмета. Оно нужно, если на одном месте хранится много вещей (как правило, в беспорядке) и если инструменты походят один на другой. Благодаря контурированию сокращается время поиска предмета и возвращения его на место.
Шаг 3. Содержание в чистоте (Сэисо)
Развиваем привычку убирать рабочее место. Утренняя уборка обычно делается за 5-10 минут до начала работы, обеденная проводится в течение 5-10 минут после обеда, также стоит задуматься об уборке по окончании рабочего дня и во время простоев.
Если нужно организовать коллективную уборку, следуйте нехитрым правилам:
- Разделите территорию на зоны, в зависимости от расположения рабочих мест и оборудования.
- Закрепите каждую зону за определенной группой людей.
- Обозначьте время уборки.
Шаг 4. Стандартизация (Сэикэцу)
Письменно закрепите правила содержания рабочих мест, технологии работы и другие процедуры. Стандартизация является необходимым условием для выполнения трех предыдущих шагов на пути к бережливому производству. Нужны инструкции по поддержанию порядка, а также новые методы контроля и поощрения сотрудников. Стандартизация может быть применена в разных направлениях: пример, как расположить мебель и оргтехнику, сколько личных вещей разрешено держать на столе и т.д.
Шаг 5. Совершенствование (Сицукэ)
Воспитывайте привычки точного выполнения правил. Педагоги часто жалуются, что дети не запоминают алгоритмы учебных, организационных действий и не применяют их на практике. Использование технологии 5S — отличная возможность продемонстрировать ученикам пользу алгоритмов и правил на собственном примере, ведь дети так или иначе копируют взрослых.
Как совершенствоваться?
- Наблюдайте за работой оргтехники, чтобы оптимизировать техобслуживание.
- Делайте фотографии «до»/»после», чтобы в полной мере оценить результат преобразований (например, рабочее место до сортировки и после)
- Прибегайте к помощи аудиторов.
- Учитывайте возрастные особенности окружающих вас людей.
- Подключите родителей: предложите им проект 5S для домашнего рабочего места ученика.
Только не доводите стремление к совершенству до абсурда. Например, маркировка шариковых ручек не создаст ничего, кроме повода для шуток.
Интеллект-карты. Полное руководство по мощному инструменту мышления
Тони Бьюзен — родоначальник методики запоминания, творчества и организации мышления с помощью интеллект-карт — подробно объясняет, что такое интеллект-карта, как она работает и как ее можно использовать в любых сферах , чтобы улучшить свою жизнь.
Купить
Визуальный менеджмент
Визуальный менеджмент — отображение полезной информации здесь и сейчас для принятия правильных решений. Мы часто сталкиваемся с визуальным менеджментом на заводах и в поликлиниках: указатели объяснят нам, как преодолеть лабиринт помещений и не попасть в нежелательные, опасные зоны.
Визуальная навигация — один из инструментов бережливого производства. В школе и детском саду она нужна детям, родителям — то есть потребителям образовательных услуг. Если в образовательном учреждении несколько входов, корпусов, то необходима внешняя навигация. Внутри, соответственно, организовывается внутренняя навигация. Ориентируясь на детей, лучше использовать не буквенные и цифровые обозначения, а рисунки. Из указателей можно сделать настоящее украшение помещений!
Отдельное внимание стоит уделить визуальной разметке пространства: разделительным линиям, линиям открытия и закрытия дверей, линиям зон безопасности. Любая разметка должна быть стандартизирована:
Раз зашла речь об удобстве детей и родителей, стоит задуматься о клиентоориентированном дизайне помещений. Навигация — лишь его часть. Чтобы действительно вывести свою учебную среду на новый уровень, старайтесь использовать в пространстве дидактические элементы, создайте зону выполнения домашнего задания для учеников, обустройте зону комфорта для родителей с удобной мебелью, кулером, образцами заявлений и витриной ученических наград.
Внедрение любых методов — это лишь внешнее выражение настроя участников образовательного процесса. Без понимания идей бережливого производства, внутренней потребности людей в его организации, никакие методы не приживутся.
В одних школах инструменты бережливого производства уже используются во всю, в других — они пока в новинку. Делитесь своим опытом с коллегами на онлайн-площадках «Российского учебника»!